Introducción
La soldadura es un proceso de fabricación en donde se
realiza la unión de dos materiales, (generalmente metales o termoplásticos),
usualmente logrado a través de la coalescencia (fusión), en la cual las piezas
son soldadas fundiendo ambas y pudiendo agregar un material de relleno fundido
(metal o plástico), para conseguir un baño de material fundido (el baño de
soldadura) que, al enfriarse, se convierte en una unión fija. A veces la presión es usada conjuntamente con el calor, o
por sí misma, para producir la soldadura. Esto está en contraste con la
soldadura blanda (en inglés soldering) y la soldadura fuerte (en inglés brazing),
que implican el derretimiento de un material de bajo punto de fusión entre
piezas de trabajo para formar un enlace entre ellos, sin fundir las piezas de
trabajo.
Muchas fuentes de energía diferentes pueden ser usadas para
la soldadura, incluyendo una llama de gas, un arco eléctrico, un láser, un rayo
de electrones, procesos de fricción o ultrasonido. La energía necesaria para
formar la unión entre dos piezas de metal generalmente proviene de un arco
eléctrico. La energía para soldaduras de fusión o termoplásticos generalmente
proviene del contacto directo con una herramienta o un gas caliente.
Clasificación de soldadura
Se pueden distinguir primeramente los siguientes tipos de
soldadura:
Soldadura heterogénea. Se efectúa entre materiales de
distinta naturaleza, con o sin metal de
aportación: o entre metales iguales, pero con distinto metal de aportación.
Puede ser blanda o fuerte.
Soldadura homogénea. Los materiales que se sueldan y el
metal de aportación, si lo hay, son de
la misma naturaleza. Puede ser oxiacetilénica, eléctrica (por arco voltaico o
por resistencia), etc.
Si no hay metal de aportación, las soldaduras
homogéneas se denominan autógenas.
Tipos de soldadura
Soldadura por arco eléctrico
Es el proceso en el que su energía se obtiene por medio del
calor producido por un arco eléctrico que se forma en el espacio o entrehierro
comprendido entre la pieza a soldar y una varilla que sirve como electrodo. Por
lo general el electrodo también provee el material de aporte, el que con el
arco eléctrico se funde, depositándose entre las piezas a unir. La temperatura
que se genera en este proceso es superior a los 5500 °C.
La corriente que se emplea en este sistema puede ser continua o alterna,
utilizándose en los mejores trabajos la del tipo continua, debido a que la
energía es más constante, con lo que se puede generar un arco mas estable.
La corriente alterna permite efectuar operaciones de soldadura con el objeto de
trabajo en posición horizontal y preferentemente en materiales ferrosos,
mientras que la corriente contínua no presenta esas limitaciones de posición y
material.
El arco se enciende cortocircuitando el electrodo con la pieza a soldar. En esa
situación, en el punto de contacto el calentamiento óhmico es tan intenso que
se empieza a fundir el extremo del electrodo, se produce ionización térmica y
se establece el arco.
Para la generación del arco existen los siguientes tipos de electrodos:
- Electrodo
de carbón: En la actualidad son poco utilizados, el electrodo se utiliza
sólo como conductor para generar calor, el metal de aporte se agrega por
separado.
- Electrodo
metálico: El propio electrodo sirve de metal de aporte al derretirse sobre
los materiales a unir.
- Electrodo
recubierto: Los electrodos metálicos con recubrimientos que mejoran las
características de la soldadura son los más utilizados en la actualidad.
Las funciones de los recubrimientos son las siguientes:
- Proveen
una atmósfera protectora
- Proporcionan
escoria de características adecuadas para proteger al metal fundido
- Estabilizan
el arco
- Añaden
elementos de aleación al metal de la soldadura
- Desarrollan
operaciones de enfriamiento metalúrgico
- Reducen
las salpicaduras del metal
- Aumentan
la eficiencia de deposición
- Eliminan
impurezas y óxidos
- Influyen
en la profundidad del arco
- Disminuyen la velocidad de enfriamiento

La corriente que se emplea en este sistema puede ser continua o alterna, utilizándose en los mejores trabajos la del tipo continua, debido a que la energía es más constante, con lo que se puede generar un arco mas estable.
La corriente alterna permite efectuar operaciones de soldadura con el objeto de trabajo en posición horizontal y preferentemente en materiales ferrosos, mientras que la corriente contínua no presenta esas limitaciones de posición y material.
El arco se enciende cortocircuitando el electrodo con la pieza a soldar. En esa situación, en el punto de contacto el calentamiento óhmico es tan intenso que se empieza a fundir el extremo del electrodo, se produce ionización térmica y se establece el arco.
Para la generación del arco existen los siguientes tipos de electrodos:
SOLDADURA MIG Y MAG
La soldadura MIG/MAG es un proceso de soldadura por arco bajo gas
protector con electrodo consumible, el arco se produce mediante un electrodo
formado por un hilo continuo y las piezas a unir, quedando este protegido de la
atmosfera circundante por un gas inerte (soldadura MIG) o por un gas activo
(soldadura MAG).
La soldadura MIG/MAG es intrinsecamente mas productiva que la
soldadura MMA donde se pierde productividad cada vez que se produce una parada
para reponer el electrodo consumido. El uso de hilos solidos e hilos tubulares
han aumentado la eficiencia de este tipo de soldadura hasta el 80%-95%.
La soldadura MIG/MAG es un proceso versatil, pudiendo depositar el metal a
una gran velocidad y en todas las posiciones, este procedimiento es muy
utilizado en espesores pequeños y medios en estructuras de acero y aleaciones
de aluminio, especialmente donde se requiere una gran trabajo manual.
Soldadura por puntos de resistencia
Para realizar la soldadura por puntos se aplica sobre las
chapas a unir una corriente eléctrica. Esta corriente se transmite a través de
unos electrodos con una determinada presión lo que eleva la temperatura de los
materiales en ese punto a un estado pastoso en el cual se unen debido a la
presión ejercida en el procedimiento (forja).
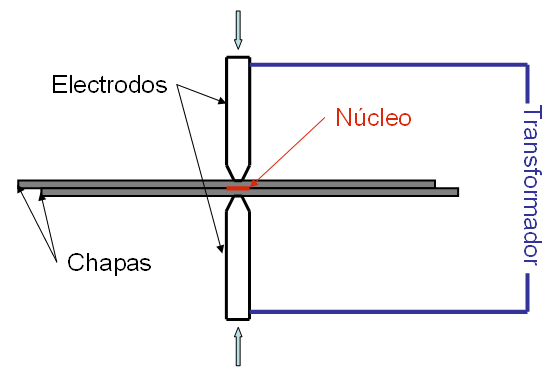
Para que la soldadura sea eficaz se deben tener en cuenta
factores como:
PRESION: Ejercer la presión adecuada,
alrededor de los diez kilogramos por milímetro cuadrado según el espesor y el
material a soldar (Para los aceros actuales este valor incrementa).
INTENSIDAD: La intensidad de la corriente debe
ser la máxima sin llegar a fusionar el material.
TIEMPO: El tiempo de soldadura debe ser corto
y siempre dependiendo del espesor del material.
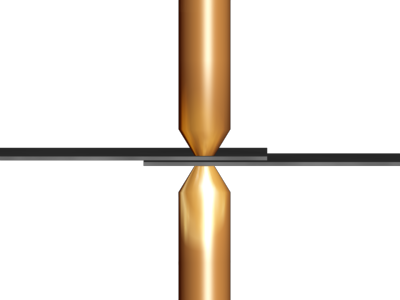
Soldadura SMAW
El arco eléctrico se mantiene entre el final del electrodo
revestido y la pieza a soldar. Cuando el metal se funde, las gotas del
electrodo se transfieren a través del arco al baño del metal fundido,
protegiéndose de la atmósfera por los gases producidos en la descomposición del
revestimiento. La escoria fundida flota en la parte superior del baño de
soldadura, desde donde protege al metal depositado de la atmósfera durante el
proceso de solidificación. La escoria debe eliminarse después de cada pasada de
soldadura. Se fabrican cientos de tipos diferentes de electrodos, a menudo
conteniendo aleaciones que proporcionan resistencia, dureza y ductilidad a la
soldadura. El proceso, se utiliza principalmente para aleaciones ferrosas para
unir estructuras de acero, en construcción naval y en general en trabajos de
fabricación metálica. A pesar de ser un proceso relativamente lento, debido a
los cambios del electrodo y a tener que eliminar la escoria, aún sigue siendo
una de las técnicas más flexibles y se utiliza con ventaja en zonas de difícil
acceso.
Soldadura TIG
En nuestros días, las exigencias tecnológicas en cuanto a
calidad y confiabilidad de las uniones soldadas, obligan a adoptar nuevos
sistemas, destacándose entre ellos la soldadura al Arco con Electrodo de
Tungsteno y Protección Gaseosa (TIG).
El sistema TIG es un sistema de soldadura al arco con
protección gaseosa, que utiliza el intenso calor de un arco eléctrico generado
entre un electrodo de tungsteno no consumible y la pieza a soldar, donde puede
o no utilizarse metal de aporte.
Se utiliza gas de protección cuyo objetivo es desplazar el
aire, para eliminar la posibilidad de contaminación de la soldadura por el
oxígeno y nitrógeno presente en la atmósfera
La característica más importante que ofrece este sistema es
entregar alta calidad de soldadura en todos los metales, incluyendo aquellos
difíciles de soldar, como también para soldar metales de espesores delgados y
para depositar cordones de raíz en unión de cañerías.
Las soldaduras hechas con sistema TIG son más fuertes, más
resistentes a la corrosión y más dúctiles que las realizadas con electrodos
convencionales. Cuando se necesita alta calidad y mayores requerimientos de
terminación, se necesario utilizar el sistema TIG para lograr soldaduras
homogéneas, de buena apariencia y con un acabado completamente liso.
Características y ventajas del sistema TIG:
- No
se requiere de fundente y no hay necesidad de limpieza posterior en la
soldadura
- No
hay salpicadura, chispas ni emanaciones, al no circular metal de aporte a
través del arco
- Brinda
soldaduras de alta calidad en todas las posiciones, sin distorsión
- Al
igual que todos los sistemas de soldadura con protección gaseosa, el área
de soldadura es claramente visible
- El
sistema puede ser automatizado, controlando mecánicamente la pistola y/o
el metal de aporte
Equipo:
El equipo para sistema TIG consta básicamente de:
- Fuente
de poder
- Unidad
de alta frecuencia
- Pistola
- Suministro
gas de protección
- Suministro
agua de enfriamiento
La pistola asegura el electrodo de tungsteno que conduce la
corriente, el que está rodeado por una boquilla de cerámica que hace fluir
concéntricamente el gas protector.
La pistola normalmente se refrigera por aire. Para intensidades
de corriente superiores a 200 Amps. Se utiliza refrigeración por agua, para
evitar recalentamiento del mango.
Soldadura láser
La soldadura por rayo láser (LBW, de laser-beam
welding) es un proceso de soldadura por fusión que utiliza la energía aportada
por un haz láser para fundir y recristalizar el material o los materiales a
unir, obteniéndose la correspondiente unión entre los elementos involucrados.
En la soldadura láser comúnmente no existe aportación de ningún material
externo. La soldadura se realiza por el calentamiento de la zona a soldar, y la
posterior aplicación de presión entre estos puntos. De normal la soldadura
láser se efectúa bajo la acción de un gas protector, que suelen ser helio o argón.

No hay comentarios:
Publicar un comentario